La vie d’un constructeur automobile n’est pas simple. Il faut sans cesse s’améliorer pour à la fois répondre à ses clients le plus vite possible, tout en optimisant les coûts. Entre la recherche, les développement, la logistique, la qualité de vie des employés, etc … il est difficile de trouver des révolutions pour parfaire les processus déjà en place.
En tant que constructeur, un des plus gros challenges est celui de la production. Une automobile est composée de milliers de pièces, qu’il faut assembler parfaitement pour assurer aux conducteurs une expérience saine et sans soucis. Les étapes sont nombreuses et doivent s’enchaîner sans heurts, et assurer parmi les milliers de combinaisons possibles pour chaque client : couleurs, jantes, options, packs, peintures, différentiation par pays et j’en passe. Pour assurer le suivi des modèles, le bon vieux code-barres ou la feuille de papier reste encore un élément de choix, jusqu’à aujourd’hui.
Suivi de production 2.0
Vous avez certainement déjà vu ça. Sur une chaîne de production, les modèles reçoivent plusieurs codes-barres pour leur identification, afin de faciliter le travail des techniciens et d’assurer le contrôle qualité. A chaque poste, le véhicule est scanné pour éviter les erreurs. Cependant, même si ce système fonctionne bien, il est perfectible. Comment faire quand le code-barres est recouvert ? Assurer un suivi jusqu’à la livraison au client ? Comment assurer la communication entre les différents pôles de production ?
Autant de questions auxquelles il est difficile de répondre. Si cela peut paraître simple à petite échelle, ça se complique dans une production de masse. Une reconnaissance sans-fil et connectée ? Simple et rapide sur le papier, mais les véhicules sont composés de métal, qui interfère avec les ondes.
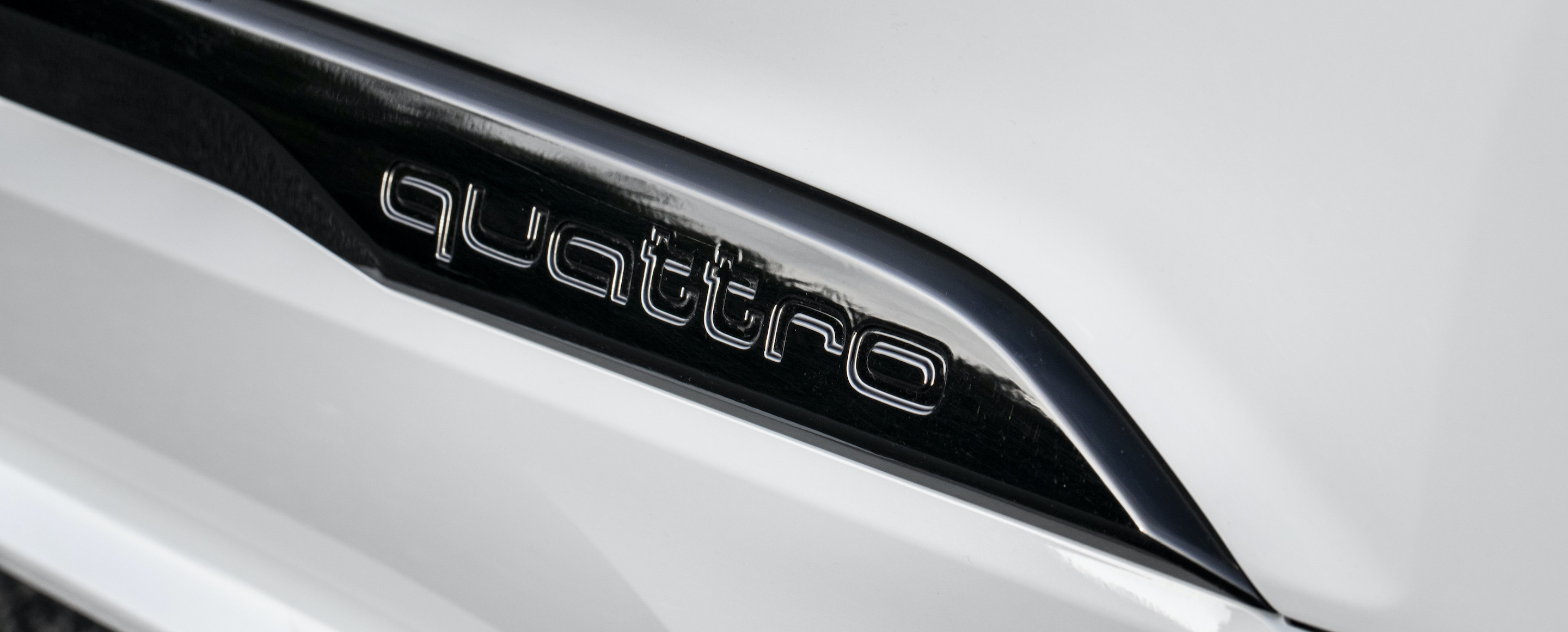
Pourtant, la solution est bien celle du sans-contact. Notamment le RFID. Pour la première fois dans le groupe VAG, les usines Audi à Neckarsulm procèdent à une identification 100% RFID des modèles en production. Dans les faits, la puce est implantée à l’arrière droit, directement sur la carrosserie. Grâce à un gros travail d’ingénierie, la puce profite du métal environnant pour rayonner et être lue par des lecteurs sans fils disposés à même la chaîne de production. Un système informatique connecté se charge de faire le lien entre le No d’identification et la carte d’identité du véhicule : modèle, options, couleurs, lieu de livraison, motorisation …
Cette puce RFID reste intégrée de la première à la dernière étape, et reste en place sur le véhicule après sa production. Pour les techniciens, cela permet un meilleur suivi et évite des opérations inutiles. Pour les équipes de qualité, cela assure un suivi parfait et un nombre moins important d’actions.
Logistique facilitée
Une fois en place, cette puce d’identification reste attachée au véhicule tout au long de sa vie. Pour les conducteurs, cela à peu d’importance, mais pour le constructeur, cette nouvelle technologie permet des opérations inédites. Dans les parcs de stockage, les véhicules pourront désormais être reconnus via des portails ou des drones, afin de les identifier facilement et faciliter leur transport.
Pour les revendeurs, même principe, on peut imaginer un petit portail à l’entrée de chaque concessionnaire, qui reconnaîtra immédiatement le véhicule, pour connaître les opérations à effectuer, les éventuelles actions qualités, et assurer un service plus personnalisé encore. Audi ouvre la porte à la reconnaissance RFID de ses modèles, et je suis sûr que de futures possibilités apparaîtront.
Photos : Audi AG
Laisser un commentaire